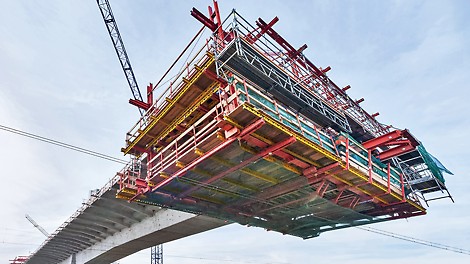

Scarica il comunicato stampa
Le immagini in dettaglio
Solid, divided building cores with lobby slabs are a feature of the customary structure in high-rise buildings. The elaborate formwork required is significantly simplified with the newly developed PERI ACS Core 400 Self-Climbing Formwork. The new type of climbing hydraulics brings big advantages through the higher speed and synchronous stroke. The special plus: continuous, simultaneous climbing of multiple cores prevents the formation of any leading edges. This considerably increases the level of safety during the execution.
High loads climbed simultaneously
The specially developed climbing hydraulics function by means of long-stroke cylinders with a lifting capacity of 40 t in each case. With a lifting height of 5.10 m, the formwork can be moved in a single step without requiring intermediate strokes, also for large storey heights. Thanks to the ample lifting capacity, large placing booms can also be climbed together with the working and climbing brackets and must not be moved separately. As a result, concreting operations are significantly accelerated as well as the elimination of additional working steps. In addition, the lifting cylinders are synchronized; even different loads, e.g. due to the component geometries, can be compensated.
Access slabs in the same working operation
The formwork itself is suitable for medium and large-dimensioned building cores whereby slabs and access levels are simultaneously concreted in one single operation. As an option, the internal formwork can be equipped with a hydraulic striking mechanism. The external formwork can be retracted a long distance thus creating optimum access for the installation of the reinforcement. The very stable working and storage areas on the inside and outside are also generously dimensioned.
Inexpensive through speed advantages and a minimum of lost parts
Short climbing cycles without intermediate strokes, simultaneous climbing of the placing boom and highly accessible working areas accelerate the work on the construction site. As a rule, 3-day cycles for each floor is possible. Furthermore, the ACS Core 400 requires only a minimum of lost parts, and the climbing anchor for the working and climbing brackets can be re-used. As is customary at PERI, most components of the climbing formwork are available from the rental parks.
Easier parapet refurbishment with PERI
New solution presented for renovation of parapets
In the civil engineering segment of bridge refurbishment, demand is already growing at a high level. Here, flexible and practical working environments are much sought-after which also make a convincing case in economic terms. The PERI solution comprising the lightweight VARIOKIT VGK Cantilevered Parapet Bracket and a suitably matched refurbishment anchor targets exactly this area of application.
At the bauma, PERI is presenting a new refurbishment anchor which, in combination with the lightweight VGK Cantilevered Parapet Bracket, is ideally suited for parapet rennovation. Bridge refurbishment presents the contractor not only with other technical but also economic challenges. Simple bracket solutions have decisive advantages if the scope of work and size of the structure does not justify complex solutions. The intended area of application is in particular short bridges with superstructures under 150 m long and having parapet dimensions of up to 60 cm wide and 100 cm high. Possible construction site workflow on the bridge structure is not affected and the flow of traffic under the bridge is also not impaired.
Practical anchoring, complete system type-tested
The multi-part VGK Cantilevered Parapet Bracket with a separate formwork unit can be manually mounted by one person thanks to a maximum component weight of 20 kg. The platform decking has no penetrations and remains closed during all work operations thus increasing the level of safety.
Another new feature is the anchor solution for subsequent anchoring on existing structures. For this, PERI uses a refurbishment anchor with a particularly high load-bearing capacity which facilitates safe working conditions through fewer anchoring points. In the process, the anchor is screwed into the drilled hole together with composite mortar whereby the undercut effect makes overhead installation significantly easier. When dismantling, the anchor bolt is simply screwed out. The anchor bolt can frequently be re-used, only the composite anchor sleeve remains as a lost component with 5 cm concrete cover in the parapet.
PERI had a type test carried out for the complete system. As a result, the VARIOKIT VGK is thus a closed solution that provides the user with a high level of safety and reliable implementation.
Specialist knowledge on demand
PERI expands customer support for bridge construction projects
Over a period of many years, an extensive range of knowledge has accumulated at PERI on a broad spectrum of civil engineering structures. As a result, the company can provide valuable assistance to its customers. In the field of civil engineering bridge construction, PERI has now established its own specialist group.
The professional expertise is there, now PERI has bundled it together for one important area: with immediate effect, a newly-founded team of experts for complex bridge building projects supports PERI customers with technical advice and planning services from one source. As a central point of contact, the group is tasked with implementing the "One Face to the Customer" concept and provides services with a short communication channel to the respective contact person. Its extensive portfolio includes project management as well as support throughout the entire project. The expert team will also find the most cost-effective solution in each case for equipment configuration on the basis of the customer´s own portfolio and PERI rental parks which are available worldwide.
The special tunnel formwork exhibit with VARIOKIT
A gallery formwork at bauma 2016
Tunnel construction and refurbishment of tunnels cannot be realized without the availability of special equipment. At bauma 2016, PERI will be exhibiting an arched formwork assembly.
A VARIOKIT arched formwork assembly for mining applications on the basis of a VARIOKIT VTC Tunnel Formwork Carriage is on display at this year´s bauma fair. The exhibit is equipped with hydraulic operating controls which largely accelerate shuttering and striking operations along with facilitating user-friendly lowering and raising of the formwork carriage. The PERI system is suitable for both mining as well as the cut-and-cover method, and reduces the installation time required for anchors through a combination of high load-bearing system walers and DW 20 anchors. Another distinctive feature of the exhibit is the transition to the portal area which includes stopend formwork. PERI also offers a large part of the VARIOKIT system for rent and thus provides the building contractor with the possibility to realize demanding projects without incurring any large investment costs.
Engineering Construction Kit for heavy-duty truss girders and shoring towers
PERI ALPHAKIT – lightweight shoring for heavy-weight bridge construction
Fewer components, simple pre-assembly, quick fitting pin connections: for bridges spans and heights up to 25 m, PERI provides an interesting solution with the lightweight ALPHAKIT Engineering Construction Kit.
Smaller bridge projects is a growth market in many regions which cannot be efficiently covered with the well-known larger and high-performance systems for shoring. For those smaller structures with spans and heights of up to 25 m, PERI is presenting in spring 2016 the ALPHAKIT Engineering Construction Kit. Special features: weight-saving design, many identical components for the truss girder and shoring tower, pre-assembly without a crane.
Reduced diversity of components, high load-bearing capacity despite lightweight construction
Where frequently a number of different profiles and connection procedures for truss girders and shoring towers are used, PERI utilizes newly developed components for the horizontal and vertical transfer of loads. A positive side effect of the new development: the deadweight of the construction could be reduced by around 30% compared to other commercially available systems. Significant cost savings can be made regarding transportation and lifting with the crane due to the weight savings.
The reduction in required components continues with the node connections that PERI uses instead of conventional screw connections. Two fitting pins are sufficient for the node connections and can be mounted very quickly.
In spite of the lightweight construction, the permissible vertical loads of ALPHAKIT lie between 240 kN/leg for 24 m tower heights and a 2.00 m x 2.00 m tower ground plan and 300 kN for a 2.50 m x 2.50 m ground plan. The permissible bending moment of a girder package is 800 kNm.
Pre-assembly on the ground without crane
PERI ALPHAKIT allows pre-assembly of complete shoring towers and truss girders on the ground and by hand whereby the low component weight and the connection technology facilitate quick and efficient working. The tower heights are continuously adjustable from 12 m to 25 m while fine adjustments are carried out by means of a head spindle with a range of +/- 75 mm. The span can be varied in 1-m increments.
Compared to conventional constructions, it is only during the erection procedure that a lightly dimensioned crane is required. The variable fields of application, simple and time-saving manual pre-assembly along with the reduction to a minimum of components with small individual weights makes PERI ALPHAKIT an attractive engineering solution in growth markets.